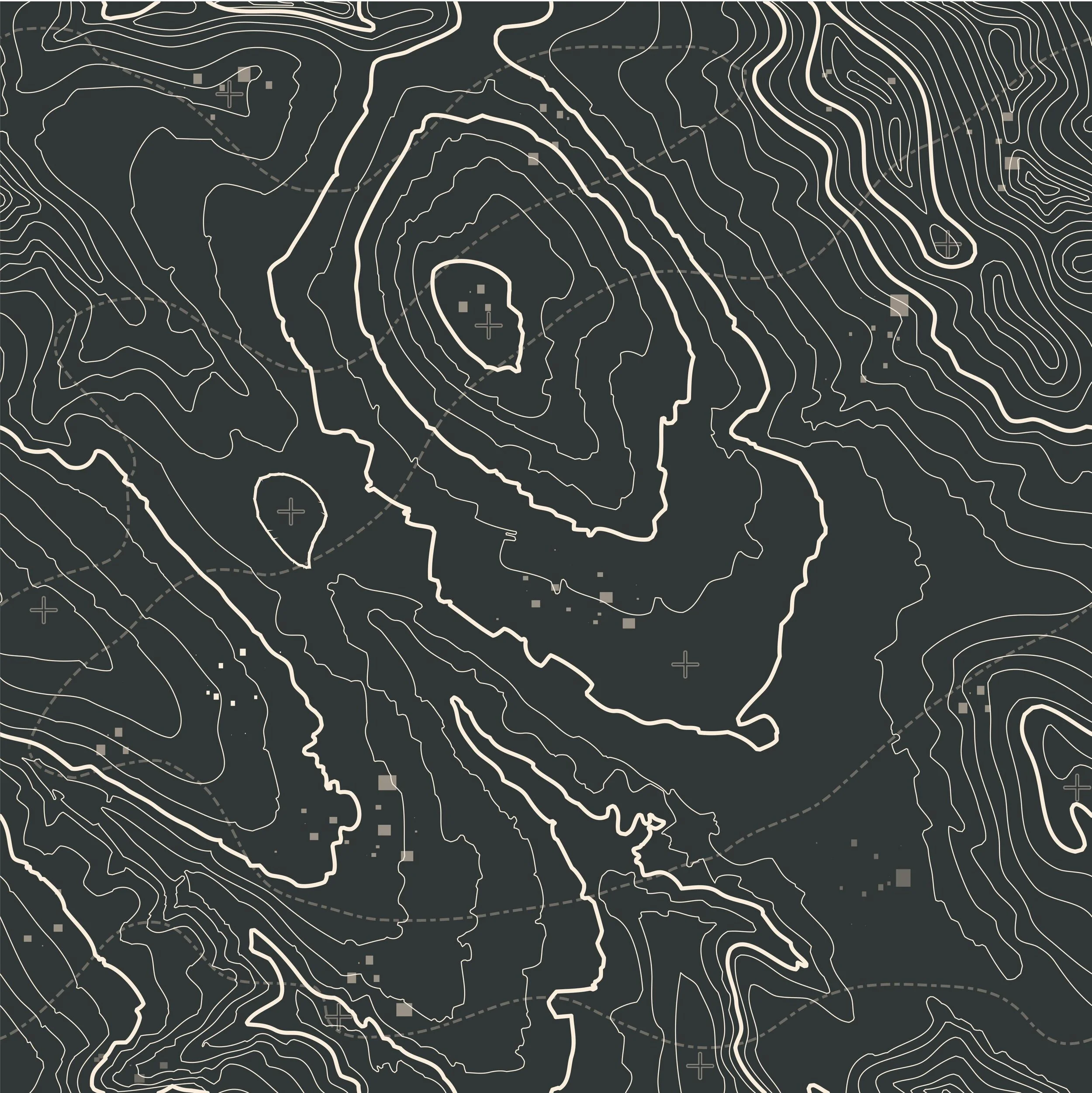
I’ve been mostly unintentionally “collecting” knives about as far back as I can remember. My dad always carried a knife, and in a way I think my interest stemmed from a desire to emulate him. From walmart keychain knives to flea market swords to the latest and greatest in “hard use” folding and fixed blade knives, I’ve had and used a little of everything.
After I separated from the Navy in 2018, I decided it was time to try my hand at making my own fixed blades. I bought a harbor freight 1X30 belt grinder and started ruining every scrap piece of metal I could find. The thing that I told myself frequently in the beginning, when I was struggling to make something that looked like a prison shank, was “do better than the last time”. That mentality has stuck with me up to this point, and likely always will.
I take a “right tool for the job approach” to design, grind geometry, and material selection, tailoring each knife to its specific role all the way down to the way the edge is sharpened. I like to cover just about any application a person could realistically need. From compact, lightweight, laser thin ground EDC knives, to robustly built outdoor use and tactical knives, I have the right tool for your job.
Knives are all freehand ground, heat treated, cryogenically treated and hardness tested 100% in house by me. All possible parts I use that I cannot currently make are sourced from US companies, with the exception of tritium vials (down to the kydex sheaths and the eyelets that hold them together). To provide a variety of the best blade alloys available today, I will source steel from foreign companies like Zapp and Bohler.
In Loving Memory,
R. Scott Carroll